With manufacturing space at minimum, machine packages have become smaller and liquid cooling has emerged as the most efficient and economical means of removing process heat. Chillers often are the only method of providing sustainable efficiency & reliability performances in "hostile" environments.
A chiller uses a refrigeration cycle to remove the collected heat from a circulating liquid. As the liquid moves through a system of tubes and pipes, it absorbs the heat generated by equipment and processes. This generated heat is then transferred by the liquid back to the chiller where it is dissipated. Fluid is cooled and sent back into the system.
>> Click here to learn more about Closed Loop Liquid Cooling Solutions.
But even if you determined that Liquid Cooling is the right solution for your environment, how do you know which heat transfer fluid you should use?
Liquids Used to Cool Your Processes
Pfannenberg process chillers offer different types of liquids to cool your processes as Water/Glycol mix, Water, and Specific Oils. Pfannenberg always recommend to use the water/glycol mixture as it's the best way to "Protect Man, Machine and the Environment".
1/ Glycol-Water Mixture
It is recommended to use a Water-Glycol
mix when freeze protection is needed, for example if the chiller is placed outdoors.
Ethylene & Propylene Glycol coolants, with proper corrosion inhibitors are available with Pfannenberg's Packaged Chillers – both full strength and pre-mixed.
We typically recommend the use of Propylene rather than Ethylene Glycol, even though Propylene has less heat transfer capability, as it is more environmentally friendly and much safer to use.
Using Glycol for indoor applications is also recommended as it deters scale and corrosion in the system and provide some lubrication to the chiller pump while protecting metals. Outdoor applications need more Glycol depending on the maximum low ambient the chiller may see. The addition of Glycol does bring capacity of the chiller down slightly.
The Glycol to Water ratio is different depending on the customer's coolant temperature needs as well as ambient temperatures being indoor or outdoor applications.
2/ Water
Depending on your installation, water cooling can be a good alternative as it is an economical and energy efficient solution. Water can be used from a local source (city water), but it is recommended to make sure that the water used is not high in mineral content which can cause corrosion or clog fluid channels. To avoid damaging the components, filtration is always encouraged.
Other types of acceptable water are: Reverse Osmosis Water (RO) and Dionized Water (DI)
- RO Water is a purified water where 90-99% of most contaminants are removed but not all ionically disolved substances.
- DI Water is water that is passed through a DI reaction chamber and has all its ions removed so all the impurities, salts or minerals that can cause corrosion are extracted.
Deionized water can sometimes be requested by customers, but it can still be damaging to certain materials and cause corrosion due to its high purity level. Indeed, due to the lack of ions, the water wants to attract ions from everything it touches. DI systems therefore require acid and caustic for regenerations and a neutralization system - which uses harsh chemicals - for the wastewater.
If highly pure water is not mandatory, RO water is a better option as the filtering process is not as defined as DI water.
In all cases, it is always recommended to contact a water treatment specialist for supervising or performing the installation and operation of water purification equipment.
3/ Oil
Cooling with oil is dedicated to very specific applications in which the process liquid is an oil or an emulsion with a high viscosity. Pfannenberg's EB Chillers allow the maximum cooling capacity in the smallest possible footprint.
These chillers are designed to handle the oil entering the evaporator at higher temperatures than in typical processes. This solution is mainly used for recirculated cooling of machinery, hydraulics, automation components, etc.
Properly selected equipment is key to cooling efficiency
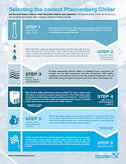
For that reason, Pfannenberg designed a 6 step guide to help you select the best chiller depending on your environment, process and type of application.
Click on the picture to open the PDF or use this link!
Have a question regarding which equipment is best for your application? Ask Us Here.